Manufacturing
We provide one-stop services,ranging from mold design and production,die casting,gravity casting,machining to surface treatment and assembly.
Zinc Die Casting Plating: Decorative and Functional
Plating zinc die cast products is typically done for one of two reasons. First is for aesthetics, providing an attractive or decorative finish to the surface of the part. Some decorative finishes can be functional, but the main purpose of a decorative finish is to be visually appealing to customers.
The second reason is more functional where parts are going to be exposed to a harsher environment or need to be more durable. A functional finish or plating is meant to improve the component performance, which can include; hardness, tarnish, UV, surface friction & corrosion resistance; along with various other attributes.
The decision to apply a functional or decorative surface finish to a component depends upon where it will be used and its function. Products that face the consumer need to be visually appealing to customers, but they also must maintain their functional performance. A faucet must look good, but also needs to resist rust and corrosion which is a means for the decorative finish to add value.

Zinc Die Casting Powder Coating and Wet Painting
A further type of surface treatment is painting. Similarly to chrome plating, on the one hand the application of a layer on a die cast surface gives an increased resistance to corrosion and wear. On the other, it plays a key role in the definition of the final visual features of the product, i.e. color and texture. Painting fulfills therefore a twofold purpose – aesthetical and functional. Even if a less homogeneous surface condition is allowed respect to chrome plating (no surface polishing process is required before applying the paint), a painted zinc die cast part has its own specific requirements and defects.
Painting at its different processes
One of the most common painting processes is spray painting, during which wet paint is applied to the part with a spray gun. Powder coating consists in the application of paint to the part as a powder layer. The paint is then cured at high temperature to obtain a thick, durable coat. Finally, cathaphoresis painting is an electrochemical process in which paint is deposited onto the part by dipping it in proper baths (as in galvanic processes). This way, the whole surface can be covered (and thus not only the areas that can be reached with a gun).
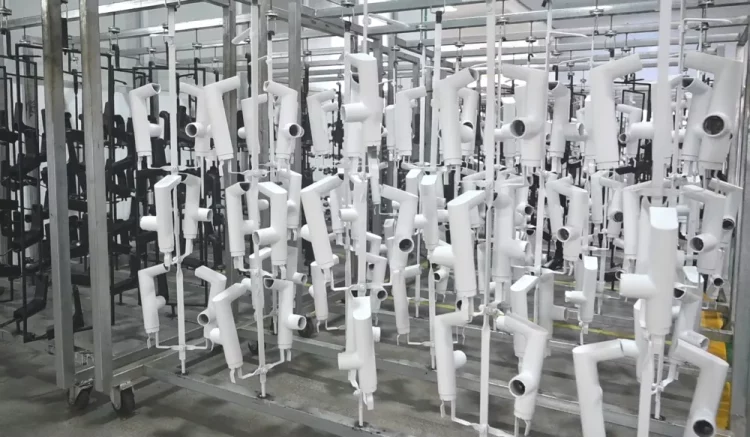
Zinc Die Casting PVD Coating
PVD stands for Physical Vapor Deposition. PVD Coating refers to a variety of thin film deposition techniques where a solid material is vaporized in a vacuum environment and deposited on substrates as a pure material or alloy composition coating.
As the process transfers the coating material as a single atom or on the molecular level, it can provide extremely pure and high performance coatings which for many applications can be preferable to other methods used. At the heart of every microchip, and semiconductor device, durable protective film, optical lens, solar panel and many medical devices, PVD Coatings provide crucial performance attributes for the final product. Whether the coating needs to be extremely thin, pure, durable or clean, PVD provides the solution.
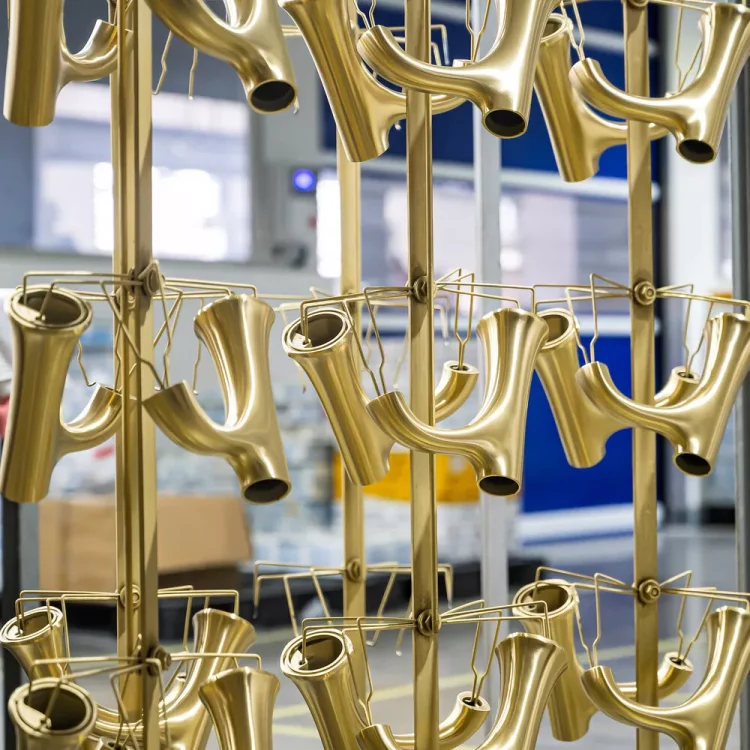
Colours of PVD treatments
Modern and contemporary shades, from black PVD to gold, from copper to bronze, scratched, matt, glossy.
The aesthetic properties of the PVD treatment are also indicated for precious elements such as jewelry, fashion accessory watches and furnishing to bring out the elegance and refinement of the treated product.
- Black
- Gold
- Copper/Bronze
- Blue
- Silver

Quick Quote
Enough is known about us. Let's talk about your project now.