Manufacturing
We provide one-stop services,ranging from mold design and production,die casting,gravity casting,machining to surface treatment and assembly.
STK Die Casting Mold Design And Manufacturing
Die casting Mold design is a key component in your project success. At STK,all of our molds start with design for manufacturing, where we talk with our customers to make sure any shortfalls for the part can be vetted and corrected before the mold is built. Modifying die features on the front end will help to improve the final part but also increase the overall quality of the tool. During this design phase, we can also predict where the tool will wear and create removable inserts for the tool that can save time and maintenance. Moreover, we know precisely how to eliminate common defects like porosity, entrained air & blisters, and surface cold shuts. So you can count on the quality of the products you will receive from STK.
Our mold division is comprised of about 25 moldmakers and 95% of them have been with STK for over 15 years. Their knowledge and experience make a tremendous difference for our customers. Not only do they make the best die cast molds but they have worked with thousands of customers from nearly every industry and can modify solutions if any issues arise during the production process.
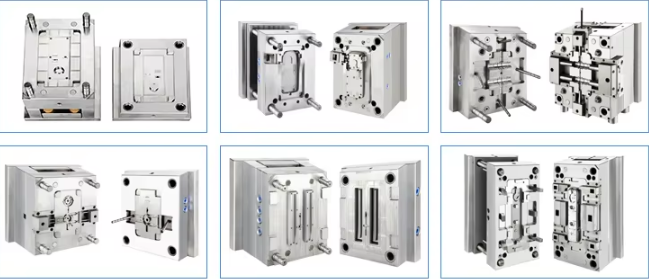
Multi-Slide Die Cast Mold
Multi-slide Molding is designed to use four (or more) perpendicular slides in the mold allowing us to create more complex and accurate castings. Multi-slide die casting offers a number of unique advantages, including:
Net shape first time, eliminating secondary operations like assembly and machining
Complex geometry and tight tolerances at high speed for world-class productivity and lower total costs
Minimum part-to-part variation compared to standard multi-cavity dies
More compact tools that are less prone to parting-line variation and its negative effect on the finished part’s dimensional tolerances
Conventional Die Cast Mold
Conventional die cast molding comes in single cavities (one part per cycle) or multiple cavities (more than one part per cycle). Our conventional tooling process is designed with only two slides rather than four and it provides customers with efficiency in production and lower costs. When you choose STK as your die casting company you receive:
Quality built dies which efficiently cope with high volume production
Attention to the design of the dies, putting in as many of the part’s features as needed to avoid secondary operations. Our goal is always net shape first time
Careful planning to eliminate machining and reduce costs
Predictive wear analysis to promote the longevity of our dies, our mold designers predict what part of the die may wear out and insert this as a separate piece of steel
Carefully planned water and cooling lines ensure efficient production
Both with new mold designs and mold transfer projects, our team has seen it all. Frequently we can adapt the existing mold to one of our die casting machines. There are instances when implementation is not easy and our team needs to be “creative” to adapt the current tool while ensuring a rapid, but also reliable solution. Our engineering and tool room professionals are proven to be dependable with many successful tooling transfer implementation projects over many years!
Our Engineering team represents the following areas
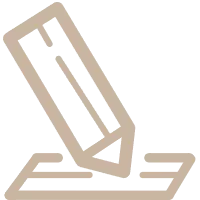
New Product Development Design
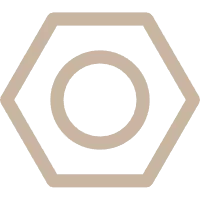
Design For Manufacturing
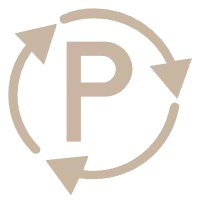
Process & Operations
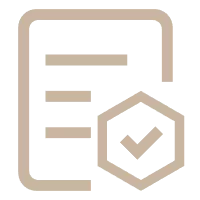
Advanced Product Quality Planning
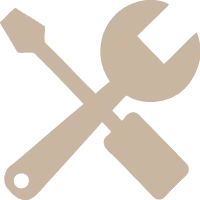
Tool Design
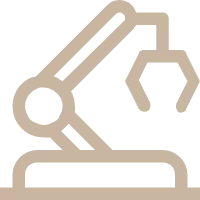
Robotics & Automation
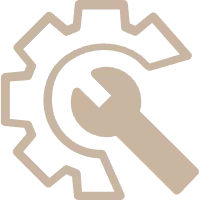
Prototyping
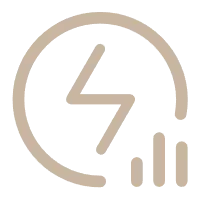
Mold Flow Analysis Simulation
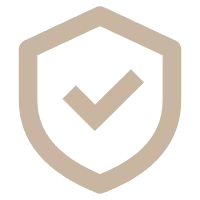
Quality Assurance & Process Control
Tooling Workshop
Quick Quote
Enough is known about us. Let's talk about your project now.