Aesthetic Considerations
In the world of manufacturing, aesthetics play a pivotal role. The surface finish of a zinc die-cast component contributes significantly to its visual appeal. Whether it’s a consumer product or an industrial part, a well-executed surface finish enhances the overall look and feel.
Functional Significance
Beyond aesthetics, the surface finish is crucial for functional reasons. It can affect properties like corrosion resistance, wear resistance, and even the ability to bond with other materials. Understanding these functional aspects is vital for choosing the right finish for a particular application.
Types of Zinc Die Casting Surface Finishes
Polishing
Polishing is a classic surface finishing technique that involves smoothing the surface of the zinc die-cast part. It provides a shiny, reflective surface, enhancing the aesthetics of the component. Polishing is commonly used when a high-gloss finish is desired. Furthermore, this technique is especially favored in situations where a sleek and reflective surface is essential for the final product.
Plating
Plating involves applying a thin layer of metal onto the surface of the zinc die-cast part. This process not only enhances the appearance but additionally improves corrosion resistance. Moreover, it ensures that the finished product not only looks aesthetically pleasing but also gains enhanced durability against corrosion. Common plating include chrome, nickel, and gold.

Powder Coating
Powder coating is a popular method whereby a dry powder is meticulously applied to the surface of the part. Subsequently, the coated part is heated, bringing forth a durable finish. This technique offers versatility, available in various colors and textures, providing both aesthetic appeal and robust protection.
Painting
Painting is a versatile surface finishing option that allows for a wide range of colors and textures. It finds common use when there is a need for specific colors or intricate designs.
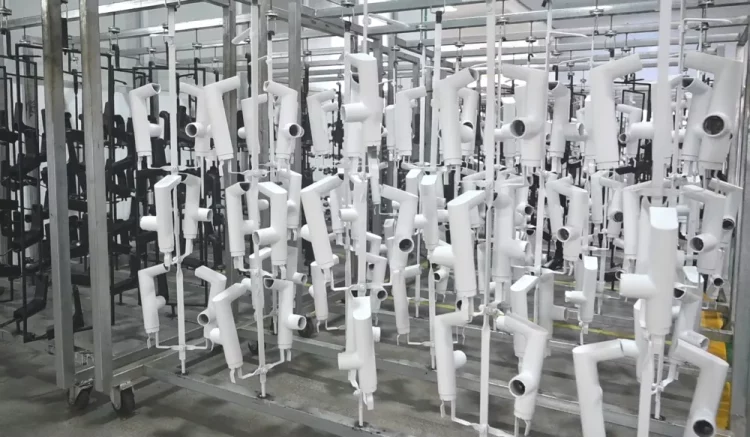
PVD Coating
PVD Coating refers to a variety of thin film deposition techniques where a solid material is vaporized in a vacuum environment and deposited on substrates as a pure material or alloy composition coating.
PVD Coatings makes zinc castings highly Durable, Corrosion and Scratch Resistant. Whether the coating needs to be extremely thin, pure, durable or clean, PVD provides the solution.
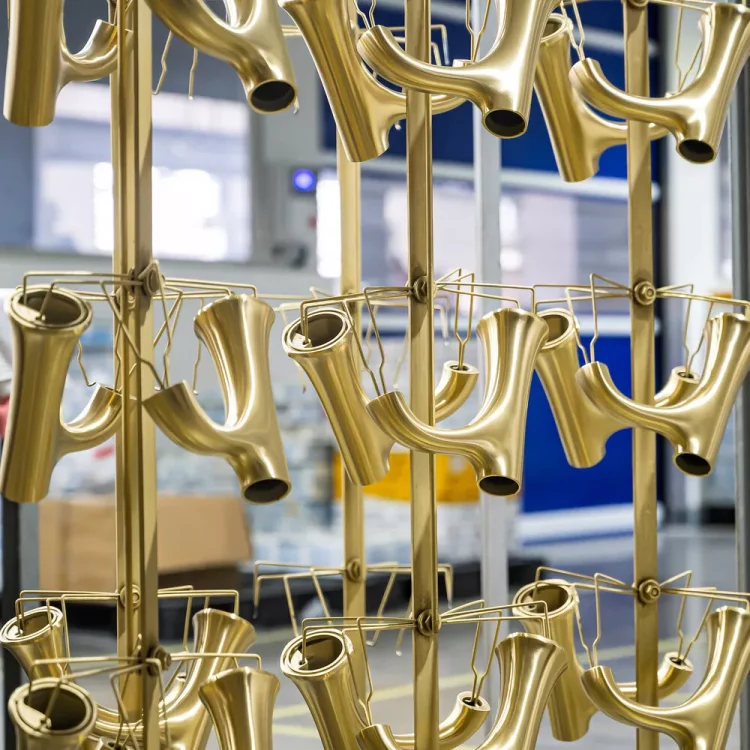
Shot Blasting
Shot blasting involves propelling abrasive particles at high speeds onto the surface of the part to achieve a textured finish. It is effective in removing surface impurities and providing a unique texture.
Electrophoretic Deposition (ED)
In the ED process, the part submerges in a paint bath, while an electric current attracts paint particles to its surface. It results in an even and consistent coating, offering excellent corrosion protection.
Passivation
Passivation is a chemical process that enhances the corrosion resistance of the zinc die-cast part. It removes free iron and other surface contaminants, creating a passive oxide layer.
Chemical Conversion Coating
This method involves applying a chemical solution to the surface, which reacts with the metal to form a protective coating. It is often used for corrosion protection and improved paint adhesion.
Tumbling
Tumbling involves placing parts in a rotating drum with abrasive media as part of a mechanical finishing process. This process smoothens the surface and removes burrs, enhancing the overall finish.
Laser Engraving
Its working principle is to control the path, power and focus point of the laser beam, so that the surface of the material is instantly heated and vaporized, melted or discolored, thereby achieving the effects of etching, cutting and marking.
Laser engraving has several advantages,High precision,Non-contact processing,Fast speed,Widely applicable materials,Strong flexibility.
In practical applications, laser engraving is often used in the field of industrial manufacturing, such as marking on electronic components and engraving patterns and texts on metal products; in the production of handicrafts, it can be used to create exquisite wood carvings, stone carvings and other works; in the advertising signage industry, it is used to make signs and display boards, etc.