Zinc Die Casting
STK Casting is a world leading precision zinc die caster.
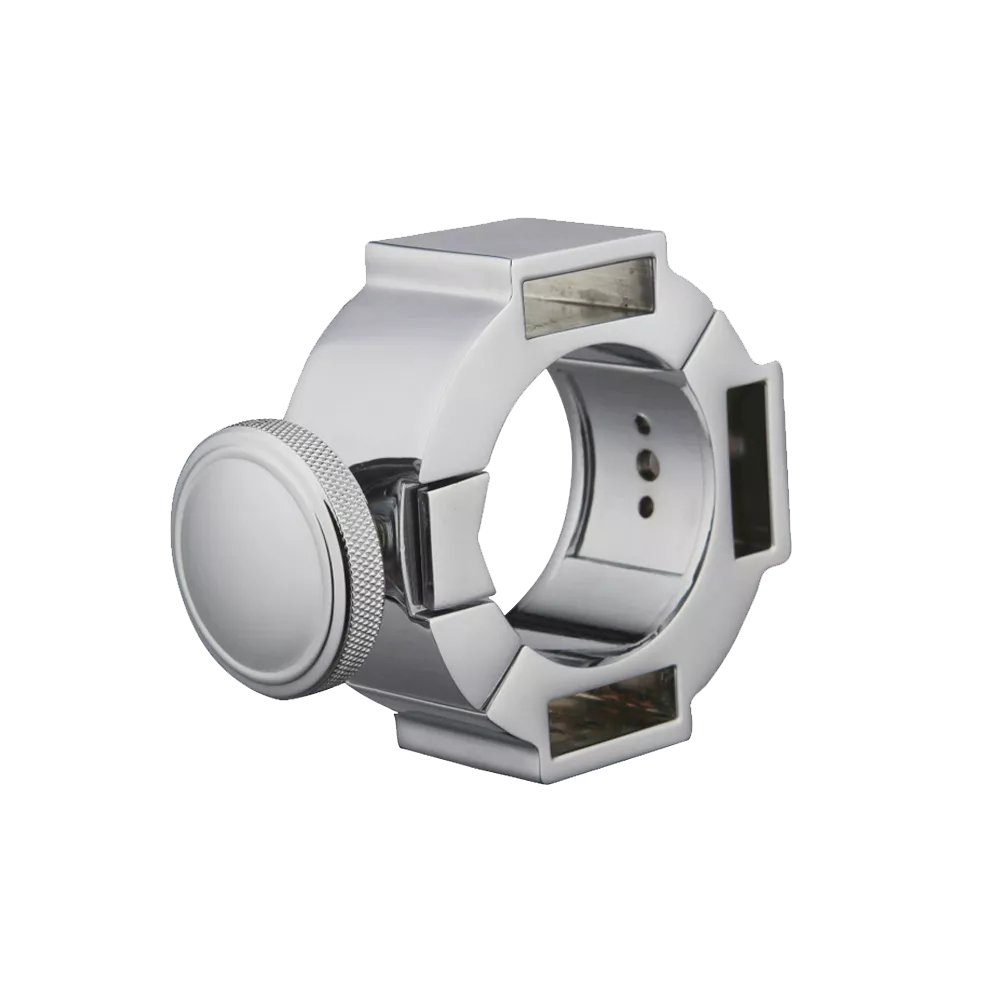
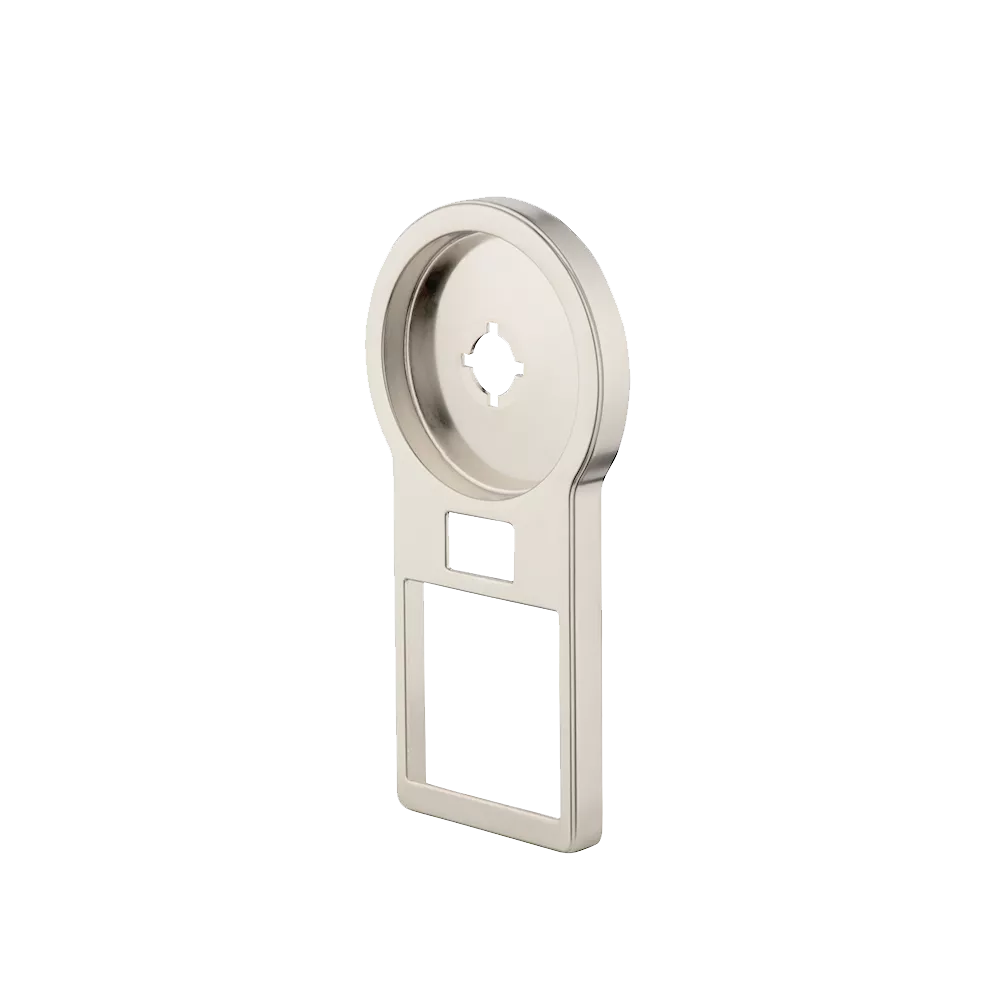
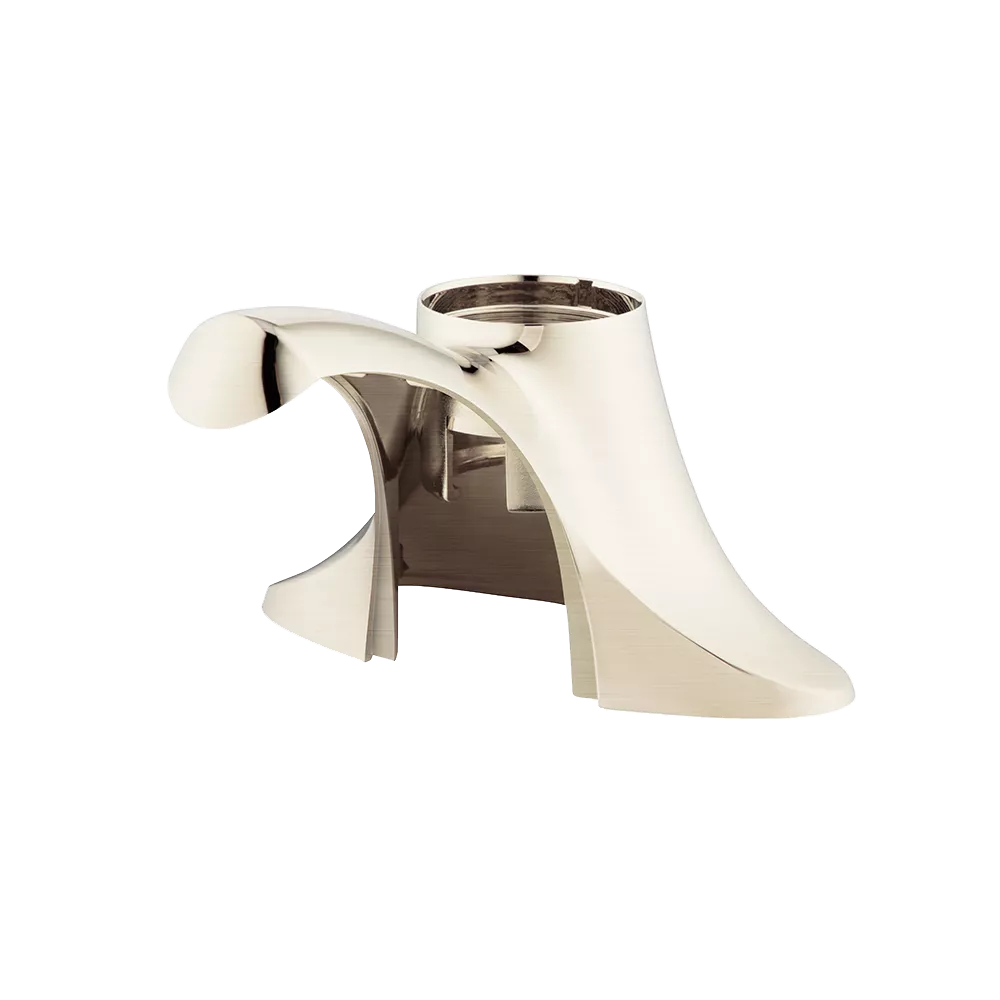
STK Casting is a world leading precision zinc die caster. We have produced billions of zinc die cast components—from one hundredth of a gram to one kilogram in size.
Applications for Zinc
- Complex net-shaped zinc housings, with precise thin walls offer excellent electrical performance and shielding properties
- Our proprietary multi-slide die casting process and superior thin-wall capabilities make us the foremost supplier of zinc components for broad range of consumer electronic devices
- The castability of zinc, its wear resistance, and structural integrity make it perfect for the creation of the multi-faceted, highly complex shapes used in automotive safety and electronics industry.
Zinc Die Casting Part Advantages
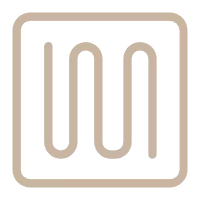
Complexe Shape

Longer Tool Life
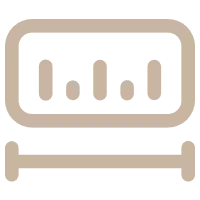
Tight Tolerances
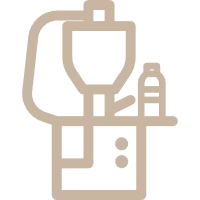
Easy Finishing
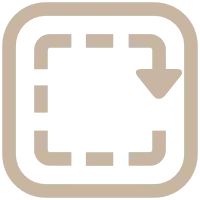
Thinner Walls
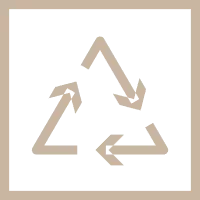
Environmentally Friendly
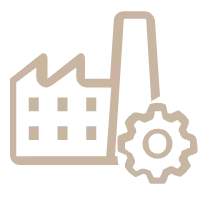
Faster Production
Complex Shapes & Tight Tolerances
Zinc die casting produces multi-cavity, complex shapes and within closer tolerances than many other production processes. In addition to producing high volume runs of virtually identical parts, it produces rugged heat and wear resistant parts that are dimensionally stable, while maintaining exceptionally close tolerances.
The die casting process gives designers the opportunity to save costs by consolidating components into one net-shape die casting. Thus, potentially eliminating secondary operations such as machining. Zinc die castings have successfully been designed as bearings (eliminating bronze alloys), rivets, and can have cast in threads. Due to these advantages, die castings are found in a wide variety of industries including automotive, building hardware, electronics, sporting goods, etc.
It should be noted that industry standard tolerances can be met and/or exceeded, if it is necessary to the design of the part. However, there are many factors that must be considered, such as; the shape of the part, where a feature is located within the tool, what is its position with other features of the part and if you are dimensioning across the parting line. When considering tool life and cost, it is best practice to allow generous tolerances and draft on areas with less fit, form or function and to tighten tolerances only in areas where it is necessary.